Vacuum coating technology is an important branch of vacuum application technology. It has been widely used in optics, electronics, energy development, physical and chemical instruments, construction machinery, packaging, civil products, surface science and scientific research. Vacuum coating methods mainly include evaporation plating, sputtering plating, ion plating, beam deposition plating and molecular beam epitaxy. In addition, chemical vapor deposition.
If the purpose of vacuum coating is to change the physical and chemical properties of the material surface, this technology is an important part of vacuum surface treatment technology, and its classification is shown in (Table-1).
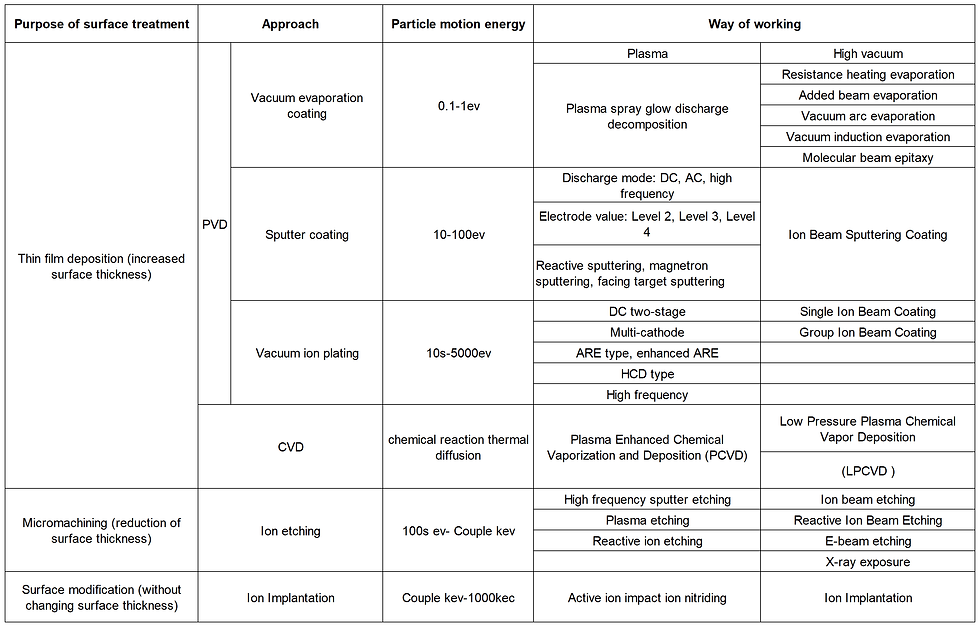
Classification of vacuum surface treatment technology (Table-1)
Vacuum technology plays a crucial role in the coating industry, especially in processes such as Physical Vapor Deposition (PVD), Chemical Vapor Deposition (CVD), and others. Here are some of the key applications:
Physical Vapor Deposition (PVD): This is a vacuum coating process that uses physical means to transfer material from a source to a substrate. Examples include evaporation (material is heated to a high temperature, and the resulting vapor condenses on the substrate to form a thin film) and sputtering (atoms are ejected from a source material and deposited on a substrate).
Chemical Vapor Deposition (CVD): Unlike PVD, this process involves a chemical reaction. Precursor gases are introduced into a vacuum chamber, where they react on the substrate surface to form a solid material. CVD is frequently used in the semiconductor industry for depositing thin films of materials such as silicon and silicon dioxide.
Atomic Layer Deposition (ALD): This is a type of CVD where layers of material are deposited one atomic layer at a time, allowing for very precise control over thickness and composition. This is achieved by sequentially introducing precursors into the vacuum chamber.
Diamond-Like Carbon (DLC) Coating: DLC is a type of PVD coating that is used to apply a layer of amorphous carbon onto a substrate. This provides the substrate with some of the properties of diamond, such as high hardness, wear resistance, and low friction.
Optical Coating: Vacuum deposition techniques are used to apply coatings to optical components like lenses and mirrors. These coatings can improve reflectivity, reduce glare, or filter specific wavelengths of light.
Thin Film Solar Cells: Thin film solar cells are made by depositing one or more thin layers of photovoltaic material onto a substrate. This is often done using vacuum deposition techniques.
Tool Coating: Vacuum processes are used to apply hard, wear-resistant coatings to tools and machine components. This can significantly extend the lifetime of the tools and improve their performance.
These are just a few examples of how vacuum technology is used in the coating industry. The ability to control the environment and process parameters precisely makes vacuum technology invaluable in these and many other applications.
Comments